At Koops, we are constantly looking for ways to improve our products, and it is with that goal in mind that we are excited to tell you about the latest addition to our Machining Department; the Computer Numerical Control Lathe – or CNC Lathe for short.
As you know, a lathe removes material by rotating a workpiece on a single axis of rotation. When controlled by a person, operating a lathe can take a good amount of time and is open to human error, creating lost manhours as well as possibly unusable pieces. We can program a sequence through the CNC Lathe that is then carried out to perfection every time, giving us maximum accuracy with minimal downtime. With the CNC Lathe's ability to sequence multiple actions, as well as its automatic tool presetter and spindle coolant system, we are able to produce high-quality parts at a rapid pace with little need for operator input.
This higher level of precision allows us to create the parts you require at a higher level of accuracy than ever before, and with a faster turnaround time. The CNC Lathe also gives us the ability to machine hardened steel components in-house, saving us the time and money that would have been lost with outsourcing the work.
All of this builds into the three promises we at Koops make to you:
Rock Solid Engineering Solutions
- The CNC Lathe improves the quality of the parts we offer
- The CNC Lathe cuts down on the time it will take to build the parts you need
- The CNC Lathe can create parts that far more accurate than a human hand could
Reliable Project Management
- The CNC Lathe allows us to create hardened steel components in-house
- The CNC Lathe increases efficiency and cuts down on labor costs
Excellent Customer Support
- The CNC Lathe gives us a new way to better meet your needs
We hope that you can see the added benefits of the CNC Lathe. Our Machining Department has always been focused on producing high-quality components at a low cost, and the capabilities of the CNC Lathe helps us achieve this goal better than ever before.
If you have any questions about the CNC Lathe or any of our other tools and capabilities, please contact our sales team at support@koops.com[:]
Headliner systems are one of the largest pieces of safety equipment in vehicles today. Dozens of individual components need to be assembled in just the right way and just the right place, so there is little room for error. The safety of the vehicle’s occupants may depend on it and the same can be said for an auto maker’s profitability. With reasons like that in mind, world-class automobile manufacturers are turning to the (HIC station) from Koops.
How Our Automated HIC Station Works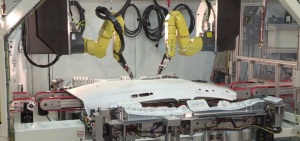
Using robotic technology, metered dispense systems, and advanced tooling design, our HIC station can help you efficiently and effectively assemble this important barrier of safety so it functions properly in the event of a roll-over accident. It also brings a variety of benefits to manufacturing headliners.
Here are the top five benefits you can count on when using an automated HIC Station from Koops, Inc.:
- Increased precision. Ensure that assembled component locations function as intended due to precise assembly.
- Consistent part-to-part cycle time. Match the broadcast rate from the plant with consistent cycle time due to automation.
- Tracking product serial numbers. Ensure that quality measures are achieved through the assembly process using serial numbers.
- Decreased scrap material. Allows all processes to be tuned to optimal parameters, reducing the scrap rate of assembled parts.
- Decreased risk of ergonomic issues. Operators do not have to interface with product during the automated cycle reducing the risk of repetitive strain injuries.
Improve Your Product and Process with an Automated HIC Station from Koops, Inc.
Long gone are the days of businesses that can be totally dependent on people to do the monotonous, rigorous, and often-times undesirable work within assembly lines. Technology has changed the nature of manufacturing over the years and changed it for the better.
Computers and robots have added great benefits to the manufacturing industry, and automation (like our HIC station) has provided a significant competitive advantage. In the world of vehicle manufacturing, this smart application of automation is especially important.
We specialize in factory automation systems at Koops and have designed and built innovative special machines and automated equipment for leading, world-class vehicle manufacturers. If you want this for your business, there is no time like the present to take the next step.
Click here to take a look and learn more about the HIC stations we have built. And if you have a headliner project, contact Koops today to discuss the benefits and awesome potential for building it all with manufacturing automation.
A successful work environment demands a combination of both employee safety and effective production. Functional standards include designs that keep employees free from injuries while allowing them to work efficiently. Automated manufacturing systems place safety first in warehouses, factories, and other environments where equipment creates potential hazards.
Machinery in the workplace often has heavy, moving parts designed to make production more efficient. These mechanical hazards present serious safety issues for employees as they use and work around the equipment. Non-mechanical hazards can also be present in these environments. Chemicals, noise, heat, and electrical dangers are common with automated manufacturing systems.
To minimize risks and keep employees safe, employers must provide thorough training, adequate protective gear, and safe access with and around equipment in the workplace. Business owners can also teach important safety tips.
- Employees should never use machinery they don't understand or have not received thorough training to use.
- Operators must follow all training procedures.
- Perform ongoing maintenance and checks of all machinery to ensure it is working properly.
- Employees should always use the correct equipment for the correct job.
- Keep guards in place at all times during operation of machinery.
- Technical personnel must follow all lock-out and tag-out procedures during maintenance.
- Wear shoes with insulated soles and wear nonconductive gloves when working with electricity.
- Do not continue to use equipment that you feel has compromised your safety system.
- Maintain emergency operational controls of equipment to ensure it shuts down in the event of an issue or accident.
- Require that all employees wear safety gear at all times.
With attention to detail and diligence to follow procedures, company owners and managers can keep automated manufacturing systems safe and productive, which benefits everyone in a company.
Photo Credit: Adam Foster